Greetings Everybody,
I am excited about where things take me in the realms of my own craft.
The idea is nothing new. The term is used, but not that often in the realms of bladesmithing, because most people have forgotten, or given up trying due to the fact that there are so many machining application available to us makers today,
that learning these skills just seem like waste of time, or something like that.
So What is "Precision Forged" ?
Just what it says. Most of the precision forged applications have been relegated to high end industry aerospace products car mechanics in the creation of motor parts etc.
It's interesting that forged blades sometimes get a bad wrap form the metallurgy community.
Most of what gets said revolved around the crystalline structure and general science about metallurgy relating to structure & carbides and less-so concerning "grain-flow" in steel.
....Metallurgy geeks can laugh at me now if you like....however, I certainly do not claim to be an expert, but have certainly studied and continue to.
What is not being talked about, is the fact that, if you take a closer look at what IS being forged, precision or otherwise,
you will find that, it's the things that are under the most stresses and heat tolerances in almost any application, that ARE being forged in one way or another.
So
Consider that!
________
OK...so.............
Fast forward to my own little world of bladesmithing.
AND
what does it mean to make a precision forged knife blade?
Well...again it's nothing new. Been done for hundreds of years.
BUT this does not mean it's easy.
Well, in fact the forging part is an acquired-skill. With enough time and patience, one can learn it. This knife is the culmination of over 10-years of hand forging blades
So....I have actually been doing it for a little while now. I did this mostly because for 7-years i did not have a grinder, so needed to get the knives very close to finished with forge hammer and anvil, then stock reduction with files.
Whether its an integral knife forged out of round or square bar (which was all I did for the first 4-years making...mostly because I love integral knives) it takes time and skill.
Most stick tang blades over 7" that will go for HT with hamon or otherwise (being slightly thicker at the end of forging) in my studio generally about 1-hour and 20-min at the forge to get right.
A "Precision Forged" blade such as the one you will see below tacks on another 20-min to half hour to the above time at the forge.
KEEPING IN MIND THAT
The part that gets tricky is doing this process with chef knives! At this time, I may be one of the few that are crazy enough to even spend the time trying this, because there will be failures in the quench.....
...other than the clean forging, it is the Heat Treatment that is the bugger.
Quenching thin blades with complex wedge-shaped geometry is a kick in the pants to say it lightly.
Keeping things straight, hoping they do not crack when doing any of the subtle straightening that will need to take place in the few seconds you have as the structures begin to set-up and as the blade cools down is a practice all it's own.
Anyhow, it's something I am playing with and plan to do more of.
Mostly, as a result of buying a grinder and seeing the sheer wast and expense of belts...laughing at myself
...though I do love my TW90
________
Here I present to you the first one I have made...I did one other blade.....but it cracked
This one is sweet!
Essentially I used no power tools on this knife save for a bit on the handle. Which is a mortised construct of rare Westinghouse round and laminated Wenge with rosin impregnated woven cotton libe...my "Tribal Wrap" treatment.
The blade was forged right to shape, thermal-cycled and heat treated and tempered.
The final edge geometry was rolled-in a bit holding a stone like a file and then sanded and polished.
The blade is 1095lm that is about 9.25" OAL is something like 14.5-15"...have not measured the whole thing yet as I am just finishing it up..sharpening etc...
I will have this one with me at G8, sharing a booth (6A) with Bawddamann Blades
Come by and check it out if you like.
Thanks for taking a look and for reading all my post.
-DON
p.s. the little red-line near the blade edge is a shadow/reflection of a priority mail box I was using as a reflector to take these images.
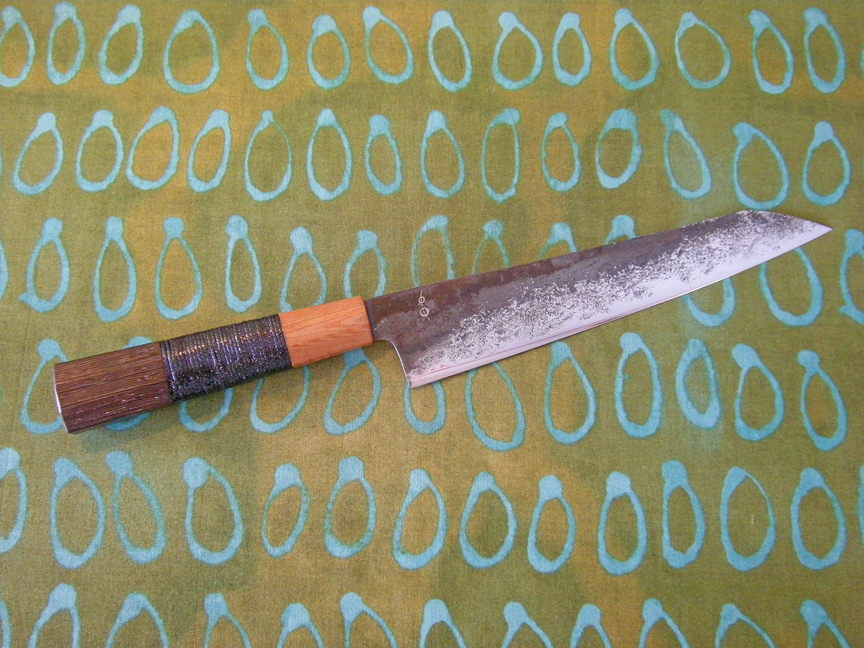
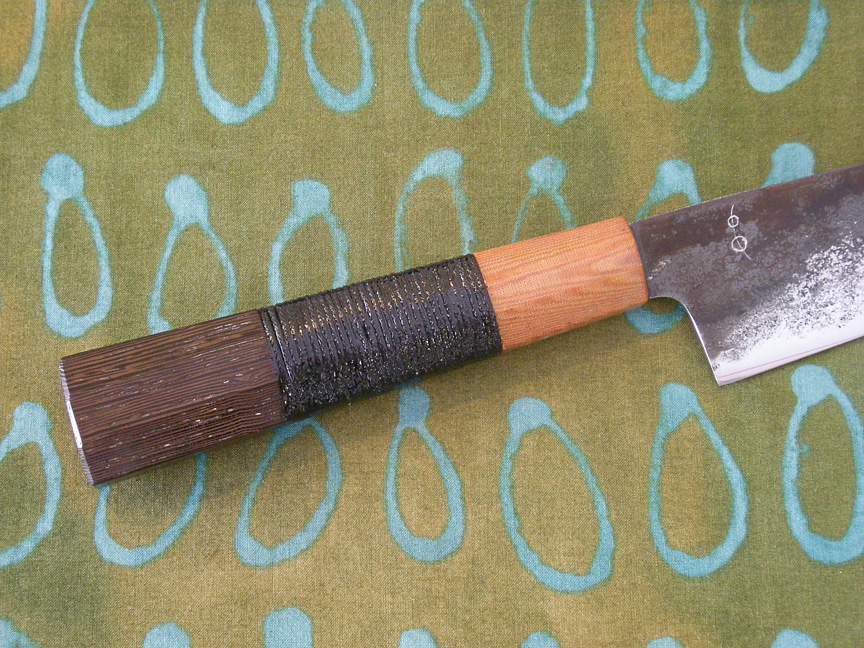
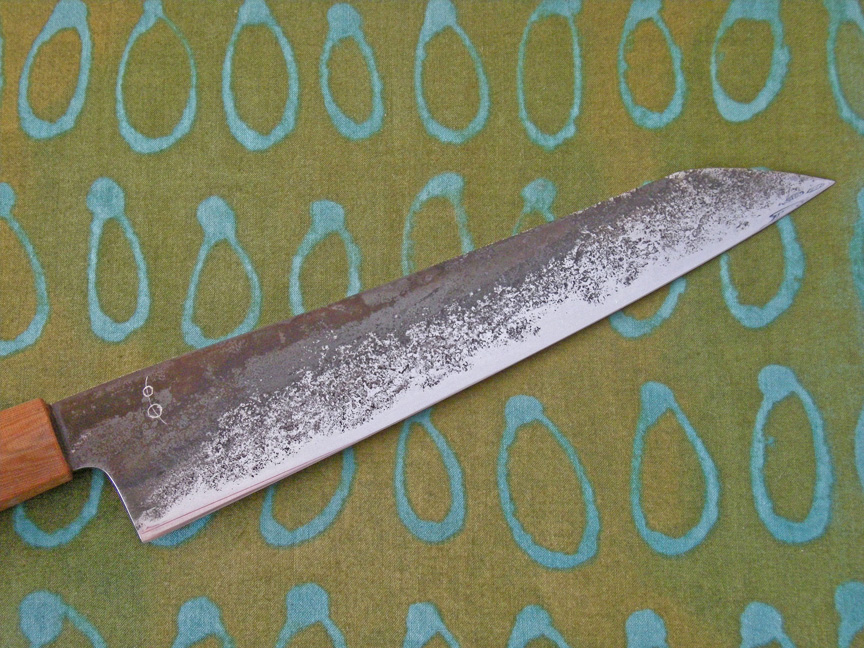

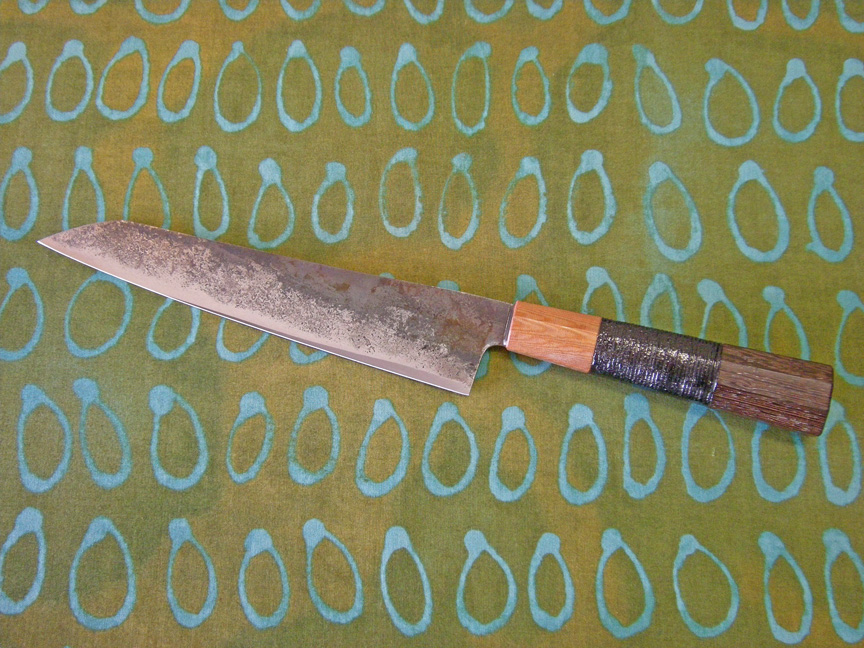